Fine work
Cylinder press for greater safety, automation and ergonomics
Hengelo-based HP Valves designs and develops flow solutions for global producers in the power generation, oil and gas, and petrochemical industries. From high-pressure valves to accessories for various applications. To meet the highest standards and functional requirements, this leading manufacturer invests in flexible, innovative machinery. The process of compressing and assembling pneumatic cylinders needed to be brought up to date. Working with Tuinte, they developed a customised semi-automatic cylinder press which has been operational since September 2020.
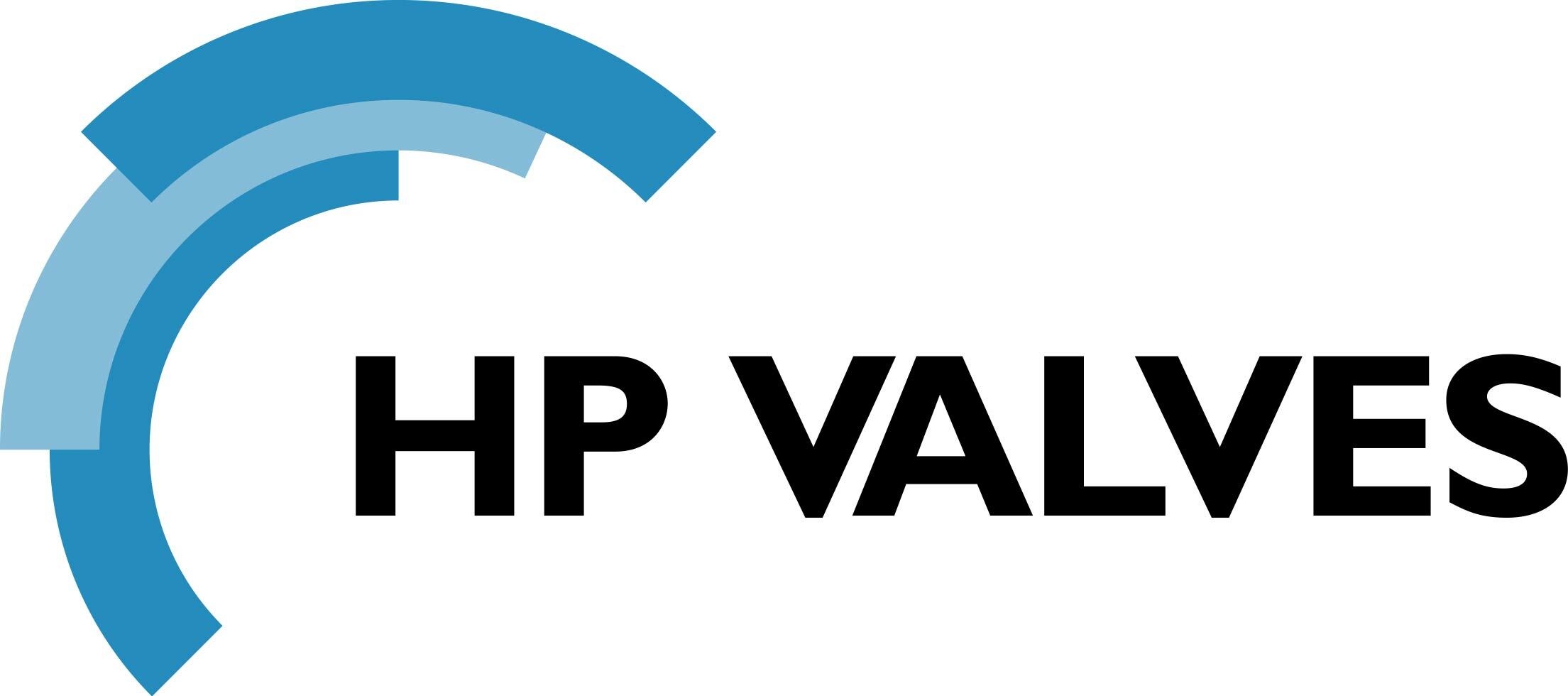
HP Valves
Mechanical engineering, Engineering machines
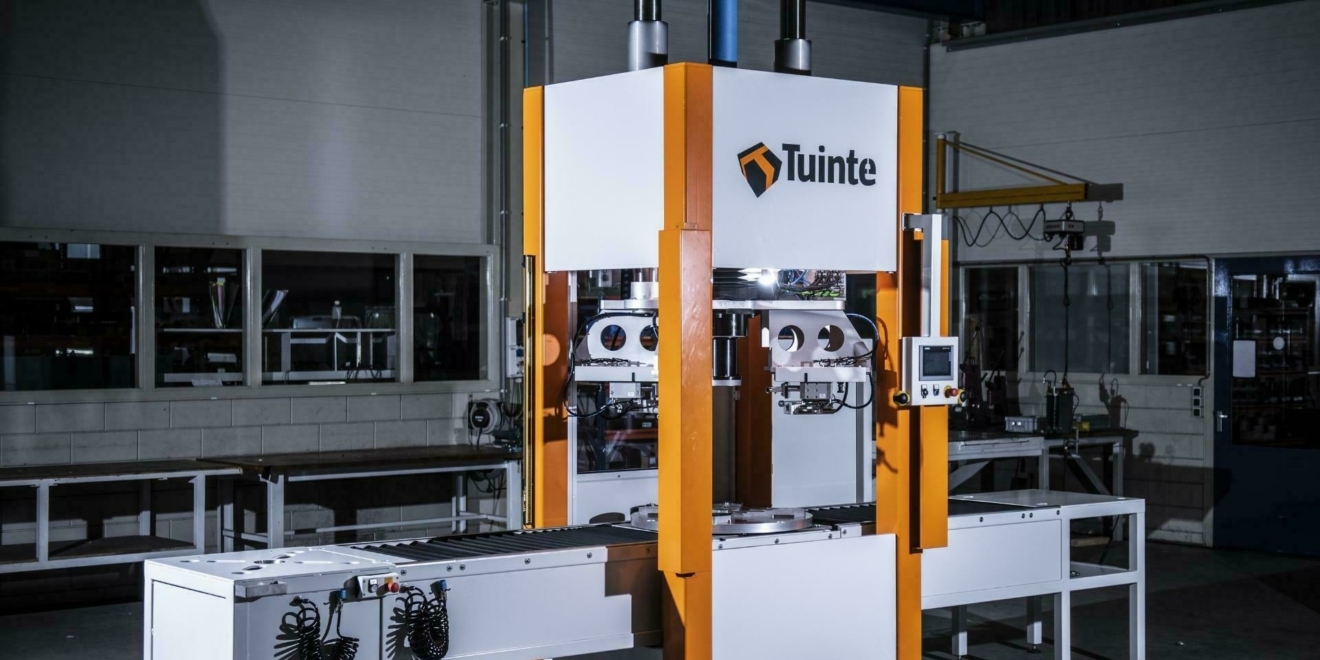
Old cylinder press
HP Valves' old cylinder press was no longer safe and ergonomic. Many operations had to be performed on and around the machine, extra tools were often needed and the necessary shielding and electrical safety devices were not in place. Looking to the future, investment was made in a new machine. Safety and ergonomics were paramount. A requirements package was submitted to several parties. Tuinte stood out from the pack and was convincing in their presentation. The company had looked into our specific product portfolio and way of working in depth, discussed with us on what was desirable and what needed to be different, and outlined the idea quite quickly."
Cooperation and feedback
Although Tuinte's engineers have a lot of experience and knowledge, in practice every project is unique. The cylinder press for HP Valves was no exception. A project team with representatives from both sides worked on an integrated solution. August is very appreciative of the cooperation. “There was constant feedback throughout the process. Tuinte visited regularly and we were in touch and consulted at every change and on completion of each project phase. Contacts with lead engineer Frank were pleasant, personal and direct. It is nice to have a single point of contact. And there were no delays to the project schedule. When the machine was delivered turn-key, we carried out the final tests at Tuinte.
Accurate, safe and automatic
Whereas the old machine needed many extra manual operations, on the new machine far more happens automatically. August van Engelen, Assembly & Paintshop Manager at HP Valves, explains: “Using a two-handed controller, we steer the parts beneath the press. This two-handed controller ensures optimal operation and improved safety. We then enter the codes, the press scans the product, the machine directs the press with the correct forces and ensures precise alignment. The main difference is that the compression of the cylinder is very controlled." The process is monitored by a safety controller using sensor solutions. The machine measures the pressure and automatically compares it against pre-set values. When a measured value exceeds those guidelines, a warning appears and action can be taken. “This way we overcome errors. Safety and ergonomics are also much better. Light screens provide shielding for the machine and a turntable allows the operator to rotate the cylinder in its compressed state. This allows him to place the studs around it easily."
Service and maintenance
Proper maintenance and regular inspection of the machine are hugely important for a reliable production process. HP Valves itself handles periodic maintenance and inspection. "We received a folder of manuals and spare parts from Tuinte. Annually, an external programmer, brought in by Tuinte from the inception of the project, visits the site to handle maintenance. Yes, we are very satisfied with the machine. We have fewer rejects and the machine is safe and accurate. We enjoy working with it. It was built exactly as we conceived it and as it was approved!"
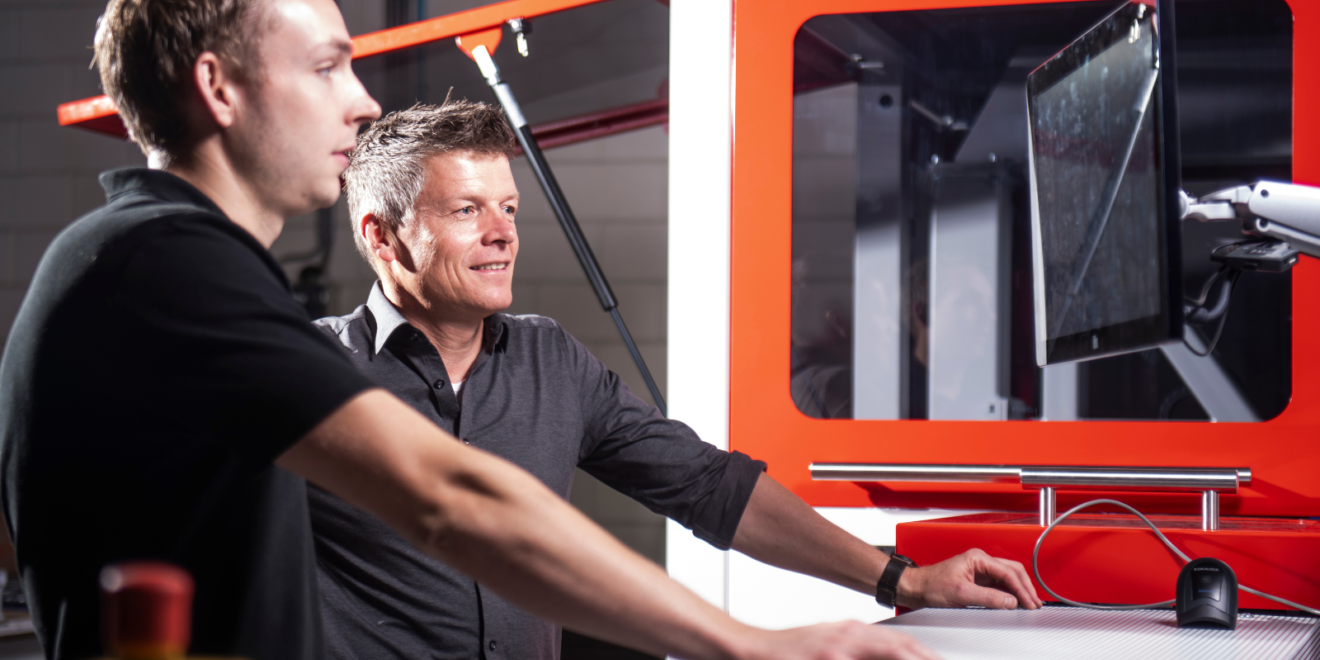